Source List Table in SAP: Understanding its Role and Functionality
In the world of SAP, managing materials efficiently is crucial for businesses.
The source list table in SAP serves as an essential tool for determining the appropriate vendors for materials within a specific plant.
By maintaining this table, companies can streamline their purchasing process and ensure they always have access to reliable supply options.
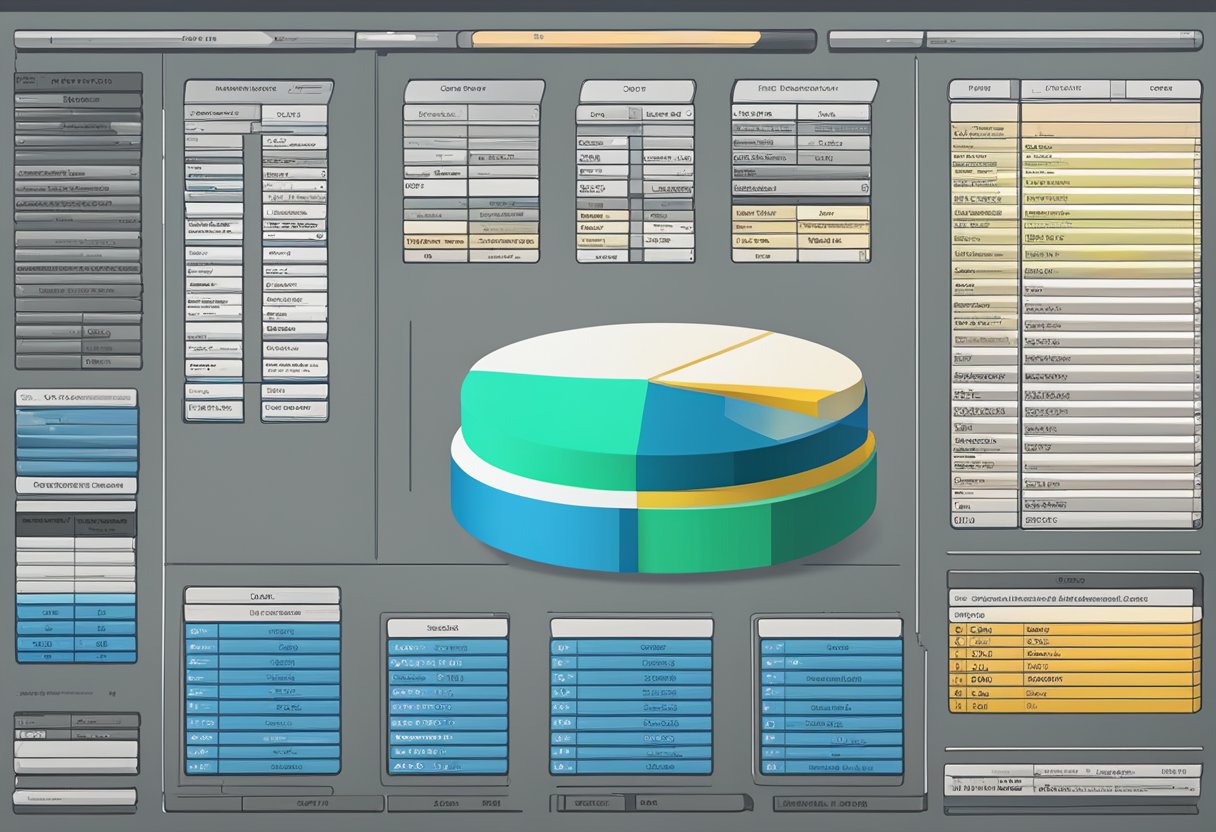
This table holds vital data about various suppliers, allowing organizations to track and evaluate potential sources of supply.
Understanding its structure and how to use it effectively can enhance purchasing decisions and improve overall supply chain management.
For those looking to navigate SAP more efficiently, grasping the functionalities of the source list table is necessary.
With a well-maintained source list table, businesses can optimize their procurement activities and maintain continuity in their operations.
Understanding Source Lists in SAP
Source lists are an essential component in the procurement process within SAP, particularly in the SAP MM module. They help define potential suppliers for materials, streamlining purchasing activities.
Their setup is crucial for maintaining efficient operations in supply chain management.
Overview of Source List
In SAP, a source list is a record that specifies the available suppliers for a material over a specific time frame. It contains details such as vendor information, purchasing conditions, and valid periods.
Each material can have a source list, which helps in automatic source determination during purchasing transactions.
Setting up a source list is linked to plant-specific requirements. To create one, certain prerequisites, like enabling the source list indicator for a material, must be met. This ensures that the correct suppliers are identified based on the needs of each plant.
Importance in SAP MM
The source list plays a vital role in the SAP MM module by facilitating organized procurement processes. It allows for automatic source selection, ensuring that the most suitable vendor is chosen based on predefined criteria.
By using a source list, companies can manage vendor relationships more effectively. It also supports quota arrangements and helps allocate orders among multiple suppliers.
This contributes to better negotiation terms and a more streamlined purchasing flow.
Integrating source lists into the procurement strategy reduces manual efforts and minimizes errors, leading to improved inventory control and efficiency in operations.
The Role of Material and Plant in Source Lists
In SAP, the material and plant play crucial roles in determining the procurement process.
Integration with the material master and the management of plant-specific source lists ensure that organizations maintain control over their supply chain.
Material Master Integration
The material master is a core component in SAP that contains essential information about all materials used in an organization.
When creating a source list, each material can have specific attributes and sourcing information defined.
Key elements include:
- Material Number: A unique identifier for each material.
- Purchasing Group: Indicates the department responsible for procurement.
- Source List Indicator: Specifies if a source list is required for that material.
This integration allows for accurate tracking of sources, ensuring that only approved vendors are selected for procurement. It helps streamline operations by eliminating unnecessary suppliers and focusing on reliable ones.
Plant-Specific Source Lists
Plants within an organization may have unique requirements based on production methods and local suppliers. Each plant can maintain its own source list to reflect these needs.
Important aspects to consider:
- Vendor Selection: Approved vendors can differ by plant, impacting availability and pricing.
- Validity Periods: Source lists can have time frames for vendor eligibility, which ensures current information.
- Automatic Vendor Selection: The system can automatically choose vendors based on the plant’s specific source list during procurement processes.
This plant-specific approach helps organizations optimize their purchasing decisions, facilitating efficient inventory management and reducing procurement risks.
Creating and Maintaining Source Lists
Creating and maintaining source lists in SAP is essential for effective material management.
Properly managing these lists allows organizations to streamline procurement processes, improve vendor relationships, and ensure compliance with supply requirements.
Manual Creation with ME01
To manually create a source list, users can utilize the transaction code ME01. This process starts by entering basic information about the material, such as the material number and the plant location.
After inputting these details, the user sets the Source List Indicator to indicate the material requires a source list.
Next, specific vendor information is added. This includes the vendor’s code, the relevant procurement details, and the validity time frame, which includes valid from and valid to dates.
Each entry can be adjusted based on changing business needs. Once all information is complete, the user clicks on the Save button to finalize the creation.
Automatic Creation Options
Automatic creation of source lists can simplify the task for users. This feature allows the system to generate source lists based on predefined criteria.
Companies typically configure settings to determine which vendors should be added automatically.
To set this up, users must define source list requirements, such as specific materials and their allowed suppliers. Once configurations are in place, the system evaluates these criteria during procurement operations, creating source lists as needed.
This method ensures up-to-date information is always available, saving time and reducing errors.
Maintaining Validity Periods
Maintaining validity periods for source lists is crucial in SAP. Each entry has defined start and end dates that indicate when the source is valid for use.
To manage this, users should regularly review and update the valid from and valid to dates. This ensures that the source list reflects current conditions and relationships with vendors.
Any changes or extensions in a vendor’s contract should also be inputted here.
Monitoring and adjusting these periods helps avoid procurement interruptions and guarantees compliance with sourcing strategies. Regular updates also help in aligning with business goals and market conditions.
Vendor Management for Source Lists
Managing vendors effectively is essential for maintaining a smooth procurement process. This involves associating the right vendors with the appropriate materials and setting up agreements that ensure timely deliveries and pricing.
Associating Vendors with Materials
In SAP, every material needs to be linked to specific vendors to create a source list. This association is crucial for streamlined procurement.
Each vendor is typically assigned a vendor number that identifies them uniquely within the system.
To associate a vendor with a material, users access the purchasing view of the material in SAP. Here, they can enter the relevant vendor number.
It’s important to maintain accurate data so that procurement teams can efficiently select vendors based on criteria like price, availability, and reliability.
Maintaining this association allows for better decision-making when sourcing materials. Companies can track vendor performance and adjust partnerships based on their evaluations, fostering a more effective procurement strategy.
Scheduling Agreements and Outline Agreements
Scheduling agreements and outline agreements are key components in vendor management. These agreements help set terms between the vendor and the purchasing organization regarding deliveries and pricing.
Scheduling agreements outline specific times for delivery, allowing firms to manage inventory levels better.
With these agreements, vendors are committed to supplying materials at predetermined intervals, thus ensuring availability when needed.
Outline agreements, on the other hand, cover general conditions for a long-term collaboration. These include pricing, quantitative commitments, and delivery terms.
They are particularly valuable for securing favorable terms with preferred vendors over a defined period.
Both types of agreements provide clarity and help in building strong vendor relationships, ensuring that both parties are aligned on expectations and deliverables.
Transaction Codes and Tables Related to Source Lists
Transaction codes and database tables are essential for managing source lists in SAP. They allow users to create, display, and maintain source lists and manage related data effectively.
Understanding these components is crucial for efficient use of SAP’s functionalities.
Tcode ME01 and Other Relevant Tcodes
Tcode ME01 is used to maintain the source list in SAP. This code allows users to create new source list entries or modify existing ones. Users must provide details such as the material number and plant.
Other relevant transaction codes include:
- ME03: Display source list.
- ME04: Change existing entries.
- ME05: Generate source lists automatically.
- ME06: Analyze the source list for proper utilization.
Each Tcode is designed for specific tasks within the source list management process, helping users quickly navigate to the function they need.
Key Database Tables Like EORD
In SAP, various key database tables are associated with source lists. One important table is the EORD table, which contains header data for the source list.
Other related tables include:
- AUFK: Order master data, which may also link to purchasing documents.
- MERE_OUTTAB_ME05: Used with Tcode ME05 for generating source lists.
Using transaction codes like SE11 and SE16, users can view these tables and their fields for analysis or reporting. Understanding these tables enhances the ability to manage procurement processes effectively.
Master Data Fields Relevant to Source Lists
Master data fields play a crucial role in managing source lists within SAP. Key fields help streamline purchasing processes, while the purchasing view provides essential insights into material management.
Key Fields in Source List Records
In SAP, the source list contains specific fields that are vital for effective material management.
Material Number is one of the primary fields, linking each entry to a unique item in the system. This ensures that all data related to a particular material is accurately tracked.
Another important field is the Source List Indicator, which determines if a source list is active for a material at a given plant. This indicator helps in managing supply relationships and availability.
Additional fields include the Validity Start and End Dates, which define the timeframe during which the source list is applicable. It is also crucial to consider the Procurement Type, indicating whether a material is sourced internally or from external vendors.
These key fields provide the framework for effective sourcing.
Using the Purchasing View for Insights
The Purchasing View in SAP offers detailed insights into the source list and material management.
Users can access various fields to gather relevant data, including pricing and supplier information.
Within the Purchasing View, the Vendor field provides essential details about the suppliers linked to the material. This enables users to evaluate supplier performance and manage vendor relationships effectively.
Additionally, the Purchasing Info Record enables users to track terms and conditions agreed with suppliers, such as pricing, delivery times, and payment terms.
This information is vital for making informed procurement decisions.
Using these fields in the Purchasing View helps streamline processes and improve overall purchasing efficiency. Understanding these aspects can strongly influence material management strategies.
Procurement Processes and Source Lists
Source lists play a critical role in enhancing procurement processes. They help organizations identify potential suppliers and support material requirements planning (MRP).
By managing approved vendors, these lists streamline the purchasing workflow and ensure timely materials are available for production.
Influence of Source Lists on MRP
In MRP, accurate data is essential for effective planning.
Source lists provide the necessary information to determine when and from whom materials should be acquired. They allow for a more precise calculation of material requirements based on lead times and supplier performance.
When a procurement plant has an established source list, it can automatically select the best vendor for each material based on availability and pricing. This reduces delays and supports timely production schedules.
The source list also aids in maintaining a balance between supply and demand, highlighting any shortages or overages in materials.
Identifying Possible Sources of Supply
Source lists contain approved vendors and alternative suppliers that meet company requirements. Each entry specifies the time period during which a material can be ordered from a given vendor.
When reviewing a source list, procurement teams can identify possible sources of supply quickly. This helps to ensure that there are always options available, reducing the risk of disruptions.
Key details, such as lead times and pricing agreements, are typically part of each entry in the list.
By regularly updating the source list, organizations can improve their material management strategies. They might evaluate vendor performance, compare pricing, and ensure compliance with contracts. This proactive approach ensures a reliable supply chain and supports efficient procurement processes.
SAP Managed Tags and Source List Indicators
Understanding SAP Managed Tags and their connection to the Source List Indicator is key for effective materials management.
The Source List Indicator plays a critical role in determining which vendors can supply materials within specific plants.
Source List Indicator and Its Significance
The Source List Indicator is a crucial element in the SAP Materials Management (MM) module. This indicator signals whether a source list requirement is in place for a material.
When set up, it ensures that a specific list of approved vendors is maintained. This helps in streamlining procurement processes.
- Importance: It prevents unauthorized vendors from supplying materials.
- Usage: A defined indicator means actions like procurement and inventory management are only performed within approved channels.
In any plant where materials are procured, maintaining this indicator is essential for compliance and operational efficiency.
It allows users to manage vendor relationships effectively, ensuring that sourcing aligns with organizational needs.